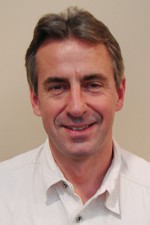
My research goal is to automate large, mobile equipment operating outdoors in unstructured environments. Examples include excavators and wheel loaders used in surface mining, windrowing machines and combines used in agriculture, continuous miners and haulage systems used in underground mining, and unmanned ground vehicles employed in military scouting operations. For the commercial machines, automation promises to increase productivity, improve safety, and reduce operational costs.
My focus is planning and perception for robots in these applications. In unstructured environments, planning is difficult due to uncertainty. Typically, the robot does not have full information about its environment before it produces a plan. Sensors are able to fill in the missing information as the plan executes, but sensor data itself can be inaccurate. Even with perfect information, robot actions can have unexpected consequences. I investigate techniques for rapidly replanning robot operations in the presence of these types of uncertainty.
The perception problems for these applications are also challenging. The robot’s environment contains irregular geometry that is difficult to represent and manipulate, such as undulating terrain, mine walls, and soil banks. Natural features, such as plants, rocks, and water puddles, combine with man-made objects to create a rich and complex environment. Adverse weather can impair the ability of the robot to sense and interpret its environment. Objects of interest may be buried beneath the soil or hidden behind a rock face. The environment can change over time as the robot interacts with it. I investigate sensors and processing techniques that can handle these conditions and extract the necessary information from the environment to perform the task.
Current projects include autonomous truck loading using excavators and wheel loaders, mining of coal, harvesting of alfalfa and other crops, and navigation of reconnaissance vehicles.
Autonomous Loading System (ALS). The goal of this project is to develop technologies to automate mass excavation with excavators and wheel loaders. In a typical mass excavation scenario, a loading machine digs material from a face and dumps the material in a truck, with a throughput of hundreds of trucks per day. The process is repetitive and continues day and night and in most weather conditions. The type of loading machine and truck can vary, as can the material to be loaded which may range from sand to hard rock. Other issues include maintaining safety of all machines and personnel in the loading area and coordination of multiple machines to achieve a prescribed goal.
Previous project work in excavation focused on the retrieval of buried objects such as ordnance or hazardous waste. The goal was to automate the task to eliminate the hazard to humans. The system used a ground penetrating radar mounted on a robotic arm to recognize and localize buried objects. Once identified and characterized, the robotic arm was able to automatically remove the overburden and retrieve the object.
Autonomous Coal Mining (USBM). The goal of this project is to automate continuous mining equipment. Thus far we have developed a complete navigation system for a continuous mining machine, including laser rangefinder-based perception for robot localization, planning for cluttered spaces, and integration and simulation tools. This system was successfully demonstrated in a real mine in West Virginia. Future work includes automated mine surveying, haulage, multiple-machine interaction, and the commercialization of these technologies.
Autonomous Harvesting (DEMETER). The goal of this project is to automate the cutting of alfalfa and other crops using a harvesting machine. DEMETER is a NewHolland 2550 Windrower retrofitted for computer control of the speed and steering functions. DEMETER is equipped with a CCD camera and on-board computer for visually detecting the line between cut and uncut crop and steering the machine to cut a crop row. DEMETER is capable of detecting the end of the row and turning to cut the next row. The machine can detect and stop for obstacles in its path. To date, DEMETER has cut alfalfa on a farm in Western Pennsylvania at a maximum speed of 4.5 mph. By the end of 1996, we plan to cut 100 acres of crop fully autonomously in California.
Unmanned Ground Vehicle (UGV). The objective of this project is to automate navigation for a military scouting vehicle. Our research vehicle, NAVLAB II, is a computer-controlled HMMWV equipped with a scanning laser rangefinder and stereo cameras for obstacle detection. For cross-country navigation, our work has focused on two capabilities: local obstacle avoidance and global navigation. We have developed a system that drove the NAVLAB II over 10 kilometers continuously while avoiding obstacles. Another system drove the NAVLAB II a distance of 1.4 kilometers to a goal location in a cluttered environment, given no initial map information. The system produced an obstacle map of the terrain it explored en route to the goal.
Research Topics
Applications
past phd students
- Barry Brummit
- Ian Davis
- M. Bernardine Dias
- Cristian Dima
- Felix Duvallet
- David Ferguson
- Juan Pablo Gonzalez
- Herman Herman
- Edward Jones
- Nidhi Kalra
- Alonzo Kelly
- G. Ayorkor Korsah
- Keith Lay
- Jacqueline Libby
- Mark Ollis
- Patrick Rowe
- Gary Shaffer
- David Silver
- Boris Sofman
- Carl Wellington
- Ling Xu
- Robert Michael Zlot