Bridge Inspection with Serpentine Robots
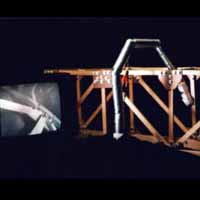
This Project is no longer active.
Federal law mandates that each bridge, spanning more than $20$ feet in America, be inspected once every two years. Currently, rigging and traffic control consumes 40-50% of the bridge inspection cost. This estimate does not consider the loss due to traffic back logs, which is significant because transportation comprises about 20 percent of the overhead cost of all goods and services in this country. Rigging and traffic control are so excessive because the inspector has to see all locations of the bridge, which are often hard to reach on large bridges. The proposed research will develop and innovative technology which resolves these short comings. Instead, an inspector, sitting in a truck on the bridge roadbed, will control a robot which can “view” the entire bridge through a sensor suite deployed at the end of the robot. This system would reduce the cost of bridge inspection, increase the safety factor, provide better views of the bridge, improve the quality of information, and as an added benefit, decrease traffic delays that are a result of such an operation.
Conventional mobile robots and robot arms cannot adequately perform bridge inspection (painting, and paint-removing) because they lack the flexibility to reach all locations in highly convoluted structures which most bridges offer. Instead, this work uses a new type of robot, termed a serpentine robot, which, as its name suggests, possesses multiple joints that give it a superior ability to flex, reach, and approach all points on the bridge.
Control of serpentine robots is difficult because a planner must account for all of the joints (degrees of freedom) of the mechanism. The coordination of these numerous joints is not handled well in traditional robot motion planning theory. Here, the robot will use a roadmap, a geometric structure used in the robotic motion planning field, to plan the paths for the robot which guarantee its sensors “see” all locations of the bridge with the sensor suite. Typically, the roadmap can be derived from a CAD model of the bridge, but if no such model exists, then the serpentine can construct the roadmap, as it inspects the bridge, from sensor data.
Currently, we are performing experiments using the JPL Serpentine Manipulator on a model bridge. We recently revamped the control hardware for the robot to run off of a Lunix box. Now, we are in the process of developing the follow-the-leader approach for the snake robot to move along the roadmap. Finally, we have uncovered some issues in computing geometric structures in symetric environments; prior computational geoemtry algorithms assume objects are located in general position, which is often not the case with man-made structures.