BendCad Modeler
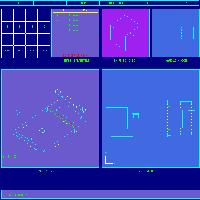
This Project is no longer active.
Bend_Cad is an in-house sheet metal design system for the Intelligent Bending Workstation Project (IBW). Traditional design practice for sheet metal part is to design the final 3D shape (usually in wire-frame representation) first, an unfolding software is then used to obtain the 2D flat pattern. BendCad adopts the “parallel design” concept to design a bent sheet metal part in both 2D and 3D domains. Designers can choose the domain which is easier for them to construct the part. A small library of parametric primitive shapes is provided as features to construct the part. Part construction is similar to CSG (Construct Solid Geometry) constructing approach. It is done by either adding (bending operation) or subtracting (punching operation) primitives shapes in the current constructing model.
BendCad resolves the ambiguity of unfolding 3D wire-frame model into 2D flat pattern and provides more feature information for further process planning. By having both 2D and 3D representations at hand at the same time, the designers consider the shapes of both the stock and the finished part while adding features to the most appropriate representation.